I've got a good way... This really only applies to those cells that use a PWM to regulate the current through them. In addition, it applies to those cells that utilize a fairly low duty cycle(<90%)...
The idea, is that when you are using a PWM, the instantaneous current through the cell is simply a function of the input voltage, divided by the cell resistance - a.k.a. Ohm's law = I = V/R. Nothing special here.
However, POWER loss(heat) is a function of the integral of the current squared. If you are feeding your cell a square wave from a PWM at 50% duty cycle, then the AVERAGE current would be, say 30A, while the maximum current for nearly 50% of the time, would be about 60A peak. When comparing the power loss of a 50% duty cycle, 60A peak square wave, to a 30A smooth current, the power loss is:
(R being the resistance of your cell)
60A peak, 50% duty = 60^2*R*(50%) = 1800*R
30A peak, 100% duty = 30^2*R*(100%) = 900*R
In other words, if you are using a 50% square wave, your power loss is roughly TWICE as much as if you were using half the current, but a smooth signal.
Since the amount of HHO is a function of how much charge passes through the cell(current * time), we can safely say that the two schemes listed above should produce about the same amount of HHO. Since we are making the same amount of HHO, and the power is reduced using the second method, we can also say that our MMW will be better as well!
So, how do we smooth the current??? Pretty easily, it turns out. Using an power inductor and a single high current diode, we can manage to smooth the current to a pretty fair degree. However, there will be SOME additional power loss in the inductor and diode, but this should be minimal when compared to the gain by using this method.
To understand what needs to be done, you may want to research what an inductor and/or a diode is. A diode essentially allows current to pass one way through it. An inductor resists changes in current, so if current is flowing through it, by god, that current will keep flowing through it(for a while...). Using the inductor, we can set up a fairly constant current, by means of a PWM. To do this, the PWM frequency will need to be set fairly high(frequency depending on the value of inductance used).
The circuit is attached. More to come later, but I've got a date.
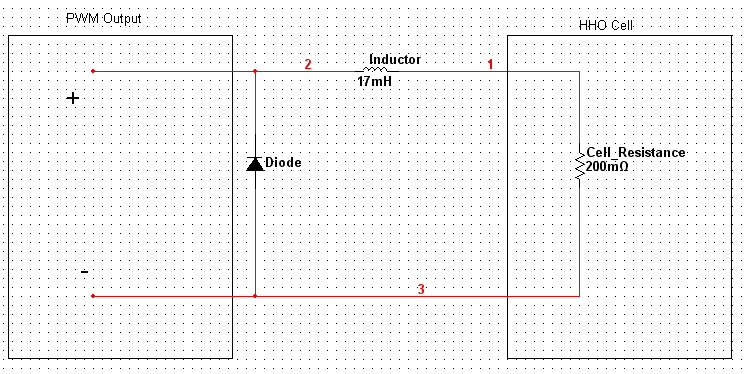